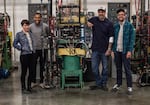
From left, Cascade's assistant plant manager Amy Dragon, mastering engineer Adam Gonsalves, COO Mark Rainey, and CFO Steve Lanning.
Alan Sylvestre / Oregon Public Broadcasting
A trio of entrepreneurs has opened what they believe is Oregon's first vinyl record pressing plant.
is delivering orders from an industrial space in Milwaukie.
Mark Rainey, Cascade's COO, shows off the six vinyl presses he bought from a factory that closed in Quebec.
"That is 150 tons of hydraulic compression," says Rainey, smiling.
Cascade Record Pressing does not look terribly different from any other small manufacturer you find in Oregon with high ceilings and a warehouse feel. Remember: This is technology that hasn't changed since the 80s. That's when industry started mothballing its vinyl record presses in favor of CDs.
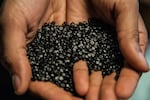
The poly-vinyl chloride compound used to made Cascade's records. Gonsalves: "It's basically made out of recycled tires."
Alan Sylvestre / Oregon Public Broadcasting
The machines start by melting down pellets of recycled poly-vinyl chloride — they look a bit like little black lentils. Heated by steam, the melted compound is extruded into a cup, forming a 180-gram biscuit that looks like a hockey puck. Then the press squashes the biscuit down flat.
The press stamps the grooves carrying song information into it, along with the label, which is stuck onto the hot vinyl as it's pressed. There's no glue.
"The labels are cured overnight before use, so all the moisture's out of them," says Rainey. "We just cure them in that old pizza oven over there."
To understand why music makers are abuzz about this, you have to know the thorny problems they face meeting the growing consumer demand for vinyl records.
Tender Loving Empire is a label based in Portland. They work with a roster of eight to 10 bands, releasing two to five vinyl releases per year. At the label's Old Town headquarters, creative director Andrew Sloan gestures to a stack of boxes in the corner.
"These 10 boxes of vinyl sitting across from us right here," says Sloan. "This is a thousand records that came back with the last two songs on Side B warped, to the point where its unlistenable. They're unsellable. It's inferior product."
Sloan says the dearth of working record presses also causes huge problems with tardy deliveries of vinyl. He approached a big factory, A To Z Media, about a new record for release in January 2014.
"A To Z comes back to me and says 'Your record won't be ready until March, the following year!'" says Sloan. "One of the major labels had decided to re-press the entire Beatles catalog, and had clogged up all the world's presses."
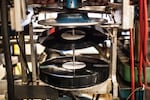
Cascade's six presses came from a plant in Montreal. Some other machines from the same factory went to other buyers.
Alan Sylvestre / OPB
Late delivery can foul up a carefully coordinated pyramid of premiers, release shows, press events, radio campaigns, distribution deals with record shops and more. While digital sales of music have overtaken physical media, CDs and vinyl still represent a bit less than half of all sales.
And the subset of vinyl sales is on the rise. Stats from the global industry interest group International Federation of the Phonographic Industry pegged vinyl sales as rising 54 percent in 2014 alone. Sloan says if Cascade is able to fill orders, he expects turnaround times for record production to drop substantially, along with shipping costs.
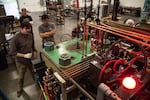
The Cascade Record Pressing plant, in Milwaukie.
Alan Sylvestre / OPB
Cascade co-founder Mark Rainey founded and ran a southern California punk rock label TKO Records for 18 years alongside the label's record store. His business partner is Adam Gonsalves, a respected audio engineer from Portland who's one of the few in the business with the equipment to cut his own record lacquers. That's a key step in the mastering process. Gonsalves was taken aback when Rainey initially tried to talk to him about starting a record press.
"My first response to that as to call the friends I had at plants, and told them to call Mark and tell him to talk him out of it," says Gonsalves.
Rainey was not easily dissuaded. He and Gonsalves started their hunt for presses.
The global supply of record presses is finite. The plants that closed did not take good care of their machines. Some were re-purposed for other uses. Others were dismantled.
Rainey and Gonsalves started searching out the last known presses that had sold. They quizzed the former owners.
Rainey says they asked a range questions.
"'How did you hear about this? Where was this? Who did you talk to?'" he says. "From there, it was tapping into the world of brokers. You're not going to be able to look them up in the phone book or anything, but they're out there. There's some in the states, Europe, the UK."
"Africa," Gonsalves chimes in. "The Carribean."
"There are a few international men of mystery," says Rainey. "It was very easy if someone else caught wind of what you were doing, especially if they had more money than you. It's be very believable for a lot to be bought out from under you with much to do. That did happen a couple times."
They finally made a winning bid — they won't say exactly how much, but somewhere well into the six figures — and delivered their first run to North Portland's Mississippi Records earlier this month. It's a re-issue of the legendary Portland punk band, Dead Moon.
Pricing for the records varies— $1.10 each for a run of 5,000 units, although the factory will do smaller orders at a higher per-unit cost.
With such an antiquated manufacturing process, the business of keeping a plant going is no small thing. More than one record press has shuttered when owners just couldn't keep production going, amid endless mechanical problems. Jeff Truhn is Cascade's maintenance chief. He's a huge guy, a former motorcycle mechanic. Truhn estimates he's been working 60 to 70 hour weeks to keep the plant rolling during the start-up phase.
"It can be very temperamental," Truhn says. "You need very specific heats and speeds and timing — even something so simple as the biscuit delivery. If it's improperly timed or something's moving too fast it can rip the labels. If the press doesn't cool long enough, you end up with round flat pieces of plastic."
Truhn says the company was fortunate to have schematics for its presses on file. He says that cuts the degree of difficulty, but the search for spare parts is still a major headache. Some parts the company simply has to have made to order.
And there's more to making records than just smashing the biscuits. Matt Earley is the founder of Gotta Groove Records, a similarly-sized plant in Cleveland, Ohio that went into business in 2009. He says often, fans think of making records as only one step.
Earley says, "The first step is the cutting of the lacquers, which is essentially, getting the music into groove format, so to speak. There are two suppliers of lacquers in the entire world. One of them, Transco, supplies, I'd say lacquers to 90% of the world. And then in the United States most of the [electro]plating is done by a third party, an independent plating company in New Jersey. There's only so many records you can plate in a given day. It's just a problem-laden process. There are so many non-human factors that cause problems down the line when you're pressing records."
Some potential customers are privately nervous about whether big labels will try to monopolize Cascade's production time.
But Gonsalves points out, with only six machines, Cascade is unlikely to get a call from Capitol Records to re-issue the Beatles. He won't rule out working for small imprints of large companies, but says the partners' preference is for small-to-mid-sized labels and artists.
"The mission is to work with those clients, because those are our people," says Gonsalves.
Cascade has taken 40 orders so far, just within a few weeks of opening its doors.